Support Your Work with Roller and Ball Bearing Stands
What's the best way to deal with the dumb end of a board? Whether it's ripping down lumber or cutting a long piece of trim on a compound miter saw, you have to have some way of overcoming the effects of gravity and leverage at the out-feed end of the operation.
If you shop around, you'll find two basic solutions: roller stands and a more recent favorite, ball bearing stands. Which one is better? As it turns out, they both have advantages in certain situations.
The ball bearing stand design has one decided advantage over a roller: it allows travel in any direction. Why is that important? To function correctly as an out-feed support, a roller stand has to be positioned so that it is exactly perpendicular to the fence - or whatever happens to be guiding the workpiece. If it's cocked even a fraction of a degree in either direction, it will "lead" the stock off course - away from the fence on one or the other end of the cut. The effect of this pull can be very hard to overcome, especially with heavy stock, and nearly impossible to control near the end of the cut, where you don't have the ability to force the stock in contact with the fence.
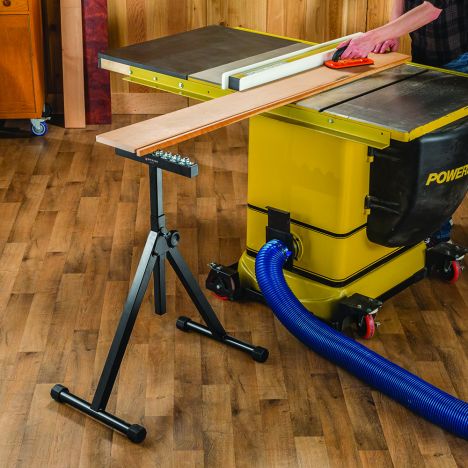
Since a ball bearing stand is "neutral" in regard to feed direction, it can be casually plunked down in any reasonable proximity to the tool and will still work just fine. But there's a drawback to the ball bearing stand as well: the space between the bearings makes this type of stand a not-so-hot choice for narrow pieces of stock, or for stock that's tipped up on its edge. When machining anything narrower than the distance between the centers of two adjacent bearings there's a nasty tendency for the out-feed o "fall off" the support. The effect is similar to the roller/feed direction problem. No matter how carefully you try to align the tip of a bearing with the intended center of the of the out-feed stock, a slight crook or bow in the stock invariably will cause it to fall off of the single support bearing and pull away from the fence at just the wrong moment.
An easy - if partial - cure for the problem is to position the row of bearings at an angle to the out-feed direction. Doing so, in effect, shortens the distance between the tips of the bearings, and gives the out-feed stock more uniform support. Using multiple rows of bearings adds to this effect. Rockler's 3-Row Ball Bearing Stand, if positioned at a slight angle to the feed direction, will produce a nearly flat out-feed support surface. A pretty good all-around bet for a variety of out-feed applications, the 3-Row stand also provides a spacious 22" x 14" top that will actually hold out-feed stock up by itself, instead of relying on the edge of the tool for one half of the support.
The good old fashioned roller stand still has its place. A roller is arguably the winner when it comes to just holding up the dumb end of a piece of lumber. A roller makes a great support for cutting trim to length on a miter saw, or drilling long pieces of stock on a drill press. In these situations, the directional alignment problem is a minor nuisance at worst, and an acceptable tradeoff for the straight, continuous support a roller provides. The same holds true for sawing and milling operations with very narrow, lightweight stock. There, the tendency of the stock to be pulled of course is fairly easy to overcome, and having a nice, straight landing spot for the out-feed stock wins out. For bench top tools and jobsite applications Rockler offers a roller support with an integrated bench clamp. This relatively compact arrangement can be clamped to any material up to 2-1/2" thick, and can be pivoted, rotated and height-adjusted to suit just about any bench-top or sawhorse supported work holding task.
In the end, the ideal outfeed work support system is to have one of each type of stand (or better, a pair of each). Thanks to Rockler's Heavy Duty Flip Top Roller Stand, you can have both in one convenient package. The Flip Top Roller Stand converts in a matter of seconds from a 14-3/4" standard roller to a support comprised of 8 ball bearings. This very handy feature gives you both of the useful types of rolling support in one tool, and also lets you switch quickly from one mode to the other with out having to adjust anything but the height.
Whatever type of stand you choose, there are a couple of general design and quality considerations that should figure in your decision. Topping the list is stability. The last thing you want from any type of stand is to have it tip over in the middle of an important procedure. Even so much as a wobble can prove disastrous when you're in the middle of a delicate cut. For that reason, buying the lightest weight stand you can find may be a mistake, even if you plan to take it with you to jobsites frequently.
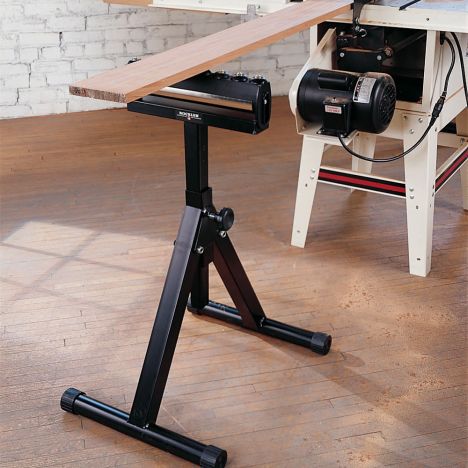
All Rockler stands are made from heavy duty square steel tubing, which helps give them their load rating of 220 lbs. for both the single row ball bearing stand and the roller stand, and an impressive 440 lbs. for the flip top and the 3-row stand. That's much more than you'll probably ever need, but the point is this: it's telling of the fact that, while still readily portable, these stands have the heft and rigidity to stay put and stay upright when you need them to.
Along with offering rock-solid stability, a roller or ball bearing stand should be easy to use and adjust. After all, it's a helping hand, and it should act like one. But not all do. Stands made from intersecting lengths of round tubing are designed so that height and leveling adjustments must be made in a single, difficult to perform operation. To further complicate matters, many stands are designed so that the very act of tightening down the height/leveling mechanism causes a change in the height adjustment.
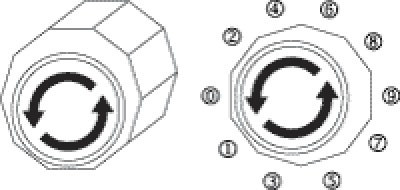
All Rockler stands, by contrast, are designed for reliable, accurate adjustments. Height and leveling adjustments are divided into two separate, easy procedures. The cross-members at the base of all Rockler stands are capped with the unique cam-action leveling system illustrated at the right. With a turn these unique foot pads, the stand can be adjusted to compensate for an out of kilter shop floor, and to accurately align with the surface of a tool. Once leveled, the height of the stand can be adjusted without affecting the angle of the support. And for added ease and accuracy, Rockler stands are equipped with a mechanism designed to prevent the height from dropping slightly during adjustments.
Roller and ball bearing stands aren't the sort of thing that draws a lot of careful thought and consideration from most of us. That seems appropriate. As "auxiliary" equipment, they should perform their function in the background - reliably, and without requiring a lot of attention or adding to the workload. To that end, Rockler roller and ball bearing stands are designed to offer worry-free stability, and to specialize in easy, accurate adjustability. And judging by what we've heard from the woodworkers who use them, they succeed in doing just that.
Keep the inspiration coming!
Subscribe to our newsletter for more woodworking tips and tricks