A Short History of Guitar Finishes
Borrowing liberally from both furniture and car coatings, guitar finishes run the gamut from edible to high-tech.
First there was the oud, a Middle Eastern instrument named after the Arabic word for wood, which led to the lute, and ultimately to the guitar. As these plucked, fretted instruments evolved, so did the finishes on them. Why? Let's look back and find out.
The lute is a very light instrument, with a thin, lively top made of softwood, like cedar or spruce. The best top woods are light, but stiff, a property called stiffness-to-mass ratio. While oil-based finishes were fine for furniture, they're not for tops. The softwood will absorb oil varnish, causing the top to become heavier but not stiffer, thus upsetting the ideal stiffness-to-mass ratio.
Glair, a mixture of egg white, sugar, honey and sometimes gum arabic, was the finish of choice for lute tops, and some makers today still use it. Made of items found in most kitchens, it is clear, nontoxic, water-based, and won’t penetrate too deeply. The egg white acts as the binder or glue to form a film and adhere to the wood, the sugar acts as a hardening resin to add durability, and the honey (or gum arabic) acts as a plasticizer to prevent it from being too brittle. Applied very thin, glair offers little protection from abrasion, but it will help shed dirt and water and keep the top looking clean.
When the modern guitar emerged in the early 20th century, it also wanted a very thin, somewhat brittle finish. French polish, which is shellac applied by pad, became the favored finish for classical and parlor guitars, and is still common on handmade classicals today. Applied in ultra-thin layers, it’s easy to keep a French polish finish thin, yet it still offers protection and a clear, glossy sheen without harming the guitar's delicate sound.
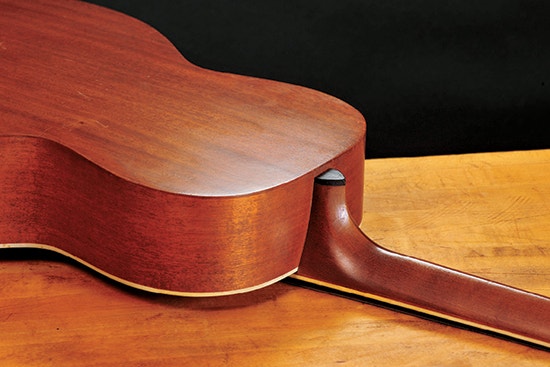
By 1920, the Jazz Age was in swing, and both nitrocellulose lacquer and spray guns had been invented, opening a range of finishing options. Meanwhile, guitars were getting bigger in order to be louder and, for the same reason, adopted metal strings. There were flat-top guitars in all sizes, from small parlor instruments to the big-bodied dreadnought, first built in 1917, and archtop guitars for another style of music and a different sound.
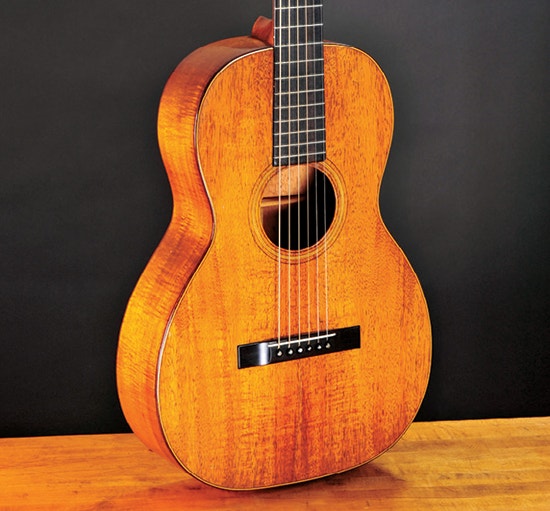
As guitarmaking went from individuals to factories, clear, high-gloss lacquer became the favorite finish for guitars. Lacquer sprays on, dries very fast, lets you apply thin layers that blend into one another seamless-ly, and lets the wood show through. However, some folks preferred added color.
Jazz and orchestral players, who favored archtop guitars for their strong mid-range chop and ability to cut through when played with a big band, often opted for so-called sunburst finishes. For that, you stain the wood in a background color, usually yellow, seal with clear lacquer, then spray one or more coats of carefully applied darker reddish or brown color around the edges to create a corona, or sunburst. When done expertly, the sunburst color visually intensifies the arch of the top.
As concert halls got bigger and microphones came into use, even the large body guitars weren't loud enough. The first electric guitar was mocked up around 1925, but within two decades some- thing very different emerged, with a decidedly new appearance and different concerns when it came to finishing.
None of the formerly critical sound issues are at play with the solidbody electric guitar. It's a thick slab of wood cut in a variety of interesting shapes, and almost any coating can go on top of it. What does matter is durability, because, let's face it, electric guitar players have a reputation for being a lot harder on their "axe" than the average classical guitarist.
They also favor a different appearance. While acoustic guitarists gravitate to clear finishes that show off the wood, electric guitar aficionados often wanted their guitars to look more like ... well, cars, to be honest. It’s no surprise that Leo Fender, whose company emerged in the 1940s, painted his guitars with brightly colored automotive paints.
Fender used DuPont's automotive lines of nitrocellulose lacquer, called Duco, and acrylic lacquer, called Lucite. He didn't even bother to change the color names. Thus, we have old Fender guitars in Duco colors like Dakota Red, Daphne Blue and Seafoam Green, and in Lucite colors like Lake Placid Blue, Olympic White and Shoreline Gold. Why, you could match your guitar color to your car, and back when I repaired guitars, I had one customer who did just that. He owned a '56 Buick and a matching turquoise Fender Stratocaster.
Car finishes became more sophisticated, and guitars followed close behind. Modern guitar finishes include linear urethane, a durable, two-part polyurethane that is easy to apply, cures fast and is relatively low in VOCs; two-part conversion varnish (also called catalyzed lacquer); cross-linked acrylics; and two- or three-part polyester finishes that are water clear and make a film as tough as your kitchen counter. In fact, the same coating may be on your kitchen counter, fiberglass boat hull and favorite guitar. Some guitarmakers today even use a hybrid approach, applying clear polyester as a base coat and filler, and topping it with repairable, easy-to-buff lacquer.
Nor are ultra-durable finishes limited to solid-body electric guitars. Our chemical prowess means we can create finishes with whatever properties we want, apply thick or thin coats, and even cure them in a variety of ways. One of the slickest curing methods is UV, or ultraviolet.
A clear, almost solvent-free finish laced with photo-reactive additive is sprayed on. The coating is then exposed to strong ultraviolet light in a particular wavelength, and it cures completely, from liquid to solid, in just seconds. Taylor Guitars helped pioneer this guitar finish, and their beautiful, great-sounding acoustics prove its worth. In fact, the coating is so durable that pickguards, invented to protect the finish, aren't even necessary.
There you have it: from simple, food-based ingredients to high-tech films, the history of guitarmaking has dabbled in them all.
Keep the inspiration coming!
Subscribe to our newsletter for more woodworking tips and tricks