Scrapers: A Simple Tool with Many Uses
Scrapers come in a variety of forms and have a variety of uses. Part of the author's collection is shown here: it includes, from left to right, a scraper for scraping interiors of hollow forms through a small opening; a large dome scraper; a straight or "boat-tailed" scraper; a diamond or "V" scraper; a form scraper for the interior of boxes; and one of a set of form scrapers for making captive rings.
Let's take an in-depth look at a simple tool: the scraper. The street view seems to be that real turners only use gouges and chisels. Nothing could be further from the truth.
The scraper is a necessary tool that continues the journey to places that a gouge or chisel cannot go. Scrapers will make a repetitive shape time and again — a great solution for making small, repetitive coves or beads in hard-to-reach areas.
Scrapers will make an undercut that a gouge cannot, such as captive rings on spindle work and bowls, or hollow forms with interiors turned through a small opening.
Finally, scrapers are the only tool that will machine a perfect fit between parts. For example, for a snap fit box lid, a scraper will turn the mortise on a box and the tenon on the lid perfectly round to the thousandth of an inch, while gouges and chisels will ride up and down with grain, making an ellipse. The scraper can remove very small amounts to achieve the machined fit, which is near impossible with gouges or chisels.
While some scrapers are made a certain shape that does not change much for the life of the tool, most are shaped to the needs of ever-changing turning situations. They are the epitome of perishable tooling: in daily shaping and sharpening, they are ground down to just shy of the tang and then thrown away.
A turning scraper works just the same as a cabinet, or card, scraper. A cabinet scraper is a 1/16"-thick rectangular piece of steel but, rather than being brought to a keen edge, about 15° of relief is filed into the edge. Then a burr is raised on the resulting fine edge with a tool called a burnisher, which is a very hard oval or round tool-steel rod with a wood handle. In use, a cabinet scraper is pushed or pulled with the burr dragging. The length of the burr limits the depth of cut to a few thousandths of an inch, which explains why the tool does not tear out in curly grain. Scrapers actually cut very slowly, a feature that makes them an extremely safe and predictable tool for woodturners.
A Woodturning Scraper
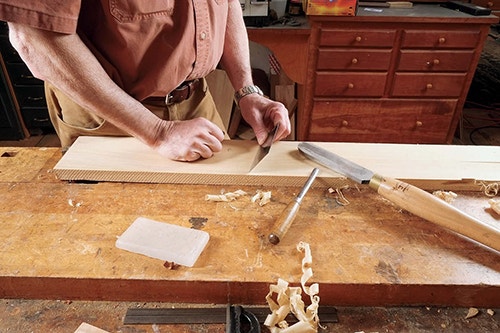
A turning scraper is much thicker than a cabinet scraper but has the same burred edge with 15° to 25° of relief under to the cutting edge. You can think of the relief as a bevel, but since a scraper is not used with a rubbing bevel, I prefer to call the ground area "relief" or "clearance." This distinguishes it from a true edged tool such as a gouge or chisel.
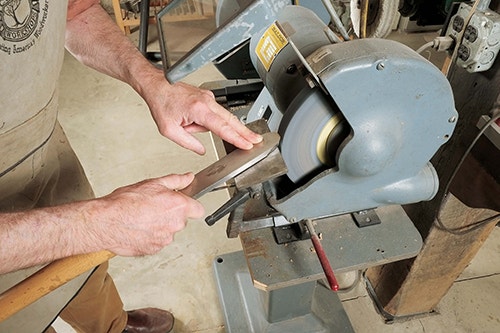
Grinding is the easiest way to raise the burr, be it carbon or high-speed steel. Simply set a grinding rest to give you the 15° to 25° of relief, place the scraper flat on the rest, and touch the edge to the wheel. It is important to immediately start moving the edge as you touch. For a straight edge, move it laterally back and forth, and for a curved edge, rotate the tool against the wheel. (Many think the tool has to be upside down to raise a burr, but this is not the case.)
The burr on a scraper forms in a process known as plastic deformation that is accomplished by either grinding or burnishing. Burnishing is direct force, while grinding is a combination of forces: the direct forward force of pushing the scraper against the wheel and the lateral force of the spinning grinding wheel in concert with the heat generated by the abrasion. Grinding forms a burr at both the top and bottom edges. The plasticity of steel drops as hardness increases, and this is why toolmakers have traditionally tempered turning scrapers to a lower measurement on the Rockwell hardness scale than chisels: about 45 on the Rockwell C (for the hardest of metals) scale.
Scrapers and Bowl Work
Because a scraper is used downhill with the burr dragging, it is beneficial to raise the tool-rest slightly in any situation; for inside bowl work, this is a necessity rather than a convenience. The tool is tilted downhill, the amount depending on the angle at which the burr is raised. Some immediate experimentation of the tilt angle as you touch the tool to the work becomes intuitive.
The scraper should be used with an extremely light touch, with very little forward force on the tool. I often hold the handle like an ink pen. Both hands work together to manipulate the tool. On inside bowl work, the scraper is often tilted on the rest to keep the burr dragging as you cut up or down the sidewall.
Finally, for bowl work, the heavier a scraper is, the better. Inertia is your friend: a heavy scraper plows through knots and bumps, while a light one goes flying. Thicker, wider and heavier is good.
Types of Scrapers
In these photos, I've pictured different types of scrapers and how they are used. For example, I choose a large dome scraper for faceplate work (especially bowls). It works equally well inside and outside. There are many specially shaped scrapers for bowl work, but I find a full half-round (dome) is the most useful and eliminates the need for all the rest.
A straight edge scraper makes things flat. I like to use a design I call a "boat-tailed" scraper, which has a bevel that prevents the scraper from leaving the line that a sharp corner can leave in its wake.
Diamond scrapers were a staple of a basic turning setup until the 1980s. The street view is that a diamond scraper is for incising lines in work, but its real purpose is to make exact fits in box lids, chucking recesses, jam chucks, tenons and the like. I call it a "chuck making scraper." The edges of this scraper are 90˚ to each other, which is great for box lids, but they are reground to less than 90˚ for inside holds for most four-jaw chucks or more than 90˚ for outside holds.
Another type, form scrapers, are ground from anything available, including many things that people throw away, to meet the needs of emerging turning situations. I make them from such things as old files, plow plane blades, screwdrivers and Allen keys.
A HSS dome scraper will cost more than $60 retail, but you can buy a 12" straight chisel for an electric chipping hammer for about $20. This can be reground to a dome and can be tilted inside a bowl better because of the hex or round shank. So: grab those screwdrivers that you see lying along the roadway!
Keep the inspiration coming!
Subscribe to our newsletter for more woodworking tips and tricks