Portable Sawmills: Lumber from Local Trees
Tired of paying high prices for lumber at the lumberyard? A portable sawmill could be your ticket to getting quality wood for your next project at a more affordable price.
I was walking around my property the other day, admiring the majestic redwood trees that grow there in abundance. Although I've never seriously considered cutting any of them down, I couldn't help but imagine how much lumber each of those big trees (many are well over 150 ft. tall and 3-1/2-ft. in diameter at the base) would yield if they were sawn. Even one or two trees could yield enough lumber for a new deck, a large shed and maybe even a kitchen's worth of cabinets (hmm…I don't suppose I'd miss just one tree...).
Evidently I'm not the only one thinking about getting lumber from local trees. Nowadays, more and more woodworkers, builders and DIYers are buying and using wood that comes from local trees sawn into lumber at a local sawmill. When you think sawmill, you’re likely imagining an old rustic building and a huge circular saw powered by an engine as big as a '56 Buick chewing through giant logs like they were toothpicks (sawdust chokes the air; the ground shakes). But the fact is that a lot of the lumber cut locally is produced by smaller portable sawmills.
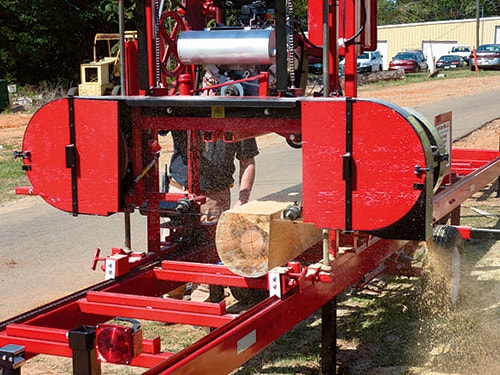
One of the earliest portable sawmills was the Mobile Dimension Mill, an ingenious device developed in the early 1960s. It uses a Volkswagen engine to power three circular saw blades: one large vertical blade, and two smaller horizontal blades that cut just ahead of it. The distance between the horizontal blades is adjustable. The motorized cutterhead travels on a track held by two end supports that suspend it above a stationary log. With each pass, the three blades produce an accurately dimensioned piece of lumber. While very efficient and productive, circular saw blade mills are large, expensive machines not designed for the casual lumber sawyer.
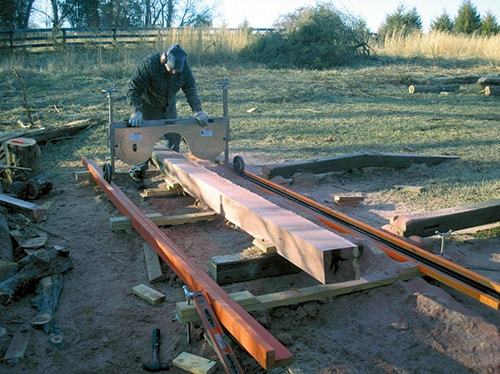
Although there are other portable lumber sawing devices out there, the machine that has proven to be the most efficient and versatile means of turning logs into high quality lumber is the portable band saw mill (PBM). These ingenious machines have a motorized horizontal band saw that rides on a track over the top of a log which remains stationary as it's cut. A PBM is small enough to be loaded in the back of a pickup or be towed behind it, yet has enough power to transform even a sizeable hardwood log into slabs, beams or boards. Compared to an old-fashioned sawmill's big circular blade, a thin band saw blade requires less power to run and creates a narrower kerf, thus producing less sawdust while yielding more useable lumber from every log. PBMs are not only safe, easy and economical to run, but since they can be transported to where trees have been felled and used to saw them right on-site, they eliminate the hassle and expense of hauling whole logs to a standard sawmill.
At least a dozen American companies currently produce portable band saw mills. Models range considerably from smaller, simpler manual models with price tags in the low-to-mid four figures to big professional models that feature built-in hydraulics and computer controls and can cost as much as a luxury automobile. They're a popular choice for a wide range of users, including: landowners who want to turn trees on their property into sellable lumber or studs, beams and planks for building barns, sheds and fences; woodworkers looking to use locally scavenged logs for their furniture and cabinets; or anyone who wants to start a business cutting other people's logs into lumber. As the price of commercially produced lumber continues to rise, more and more folks are looking for alternative ways of getting their materials from trees they have on hand. Tree stumps, branches and logs can often be garnered from neighbors, scavenged after storms and obtained from local tree cutters or power and telephone companies who cut trees threatening overhead lines.
Not only are portable band saw mills available as new machines (customized with a wide range of options to suit the purchaser's needs), but there’s a burgeoning market in used machines as well. If you don't want to invest in your own machine, there are plenty of sawyers out there who will bring their PBM to your property and saw your logs into lumber for an affordable fee. Either way, the lumber produced will be considerably less expensive than what you'd pay at a commercial lumberyard.
Portable Mill Anatomy
The heart of a portable band saw mill is a motorized, horizontally oriented band saw mounted on a carriage that rolls along a pair of rails that act as a track. The track is part of a bed with cross supports that creates a level platform for the log (or branch, plank beam, etc.) to be cut. Adjustable posts and clamps attached to the bed are used to position the log and hold it firmly in place.
During cutting, the carriage rolls over the top of the stationary log as the band saw takes a cut. The height of the blade relative to the log is adjusted by moving the entire cutterhead (band saw and motor) up or down, which sets the thickness of cut. The adjusting mechanism, called the "setworks," allows adjustments to be made in very fine increments, so that the dimension of cut boards is very accurate.
The band saws on all but the largest industrial-sized PBMs sport 19" diameter wheels that run a 1-1/4" or 1-1/2" wide blade. The distance between the wheels/blade housing determines the mill's maximum width-cutting capacity, which ranges from 24 inches to 40 inches, depending on the model.
A blade tensioning mechanism and a pair of heavy-duty guides (much like those found on a regular woodworking band saw) keep the blade running straight and true during cutting — essential for obtaining flat boards or planks. When cutting resinous woods, like pine and fir, a small plastic tank and flexible hose feeds a water-based lubricating mixture onto the blade, to help keep the blade clean and running smoothly.
A PBM may be powered by either a gasoline or diesel engine, or a large electric motor (single- or three-phase). The engines/motors on smaller models range anywhere between 7hp and 30hp, while larger models that run on big multi-cylinder engines may produce 50 horsepower or more. The more power the PBM has, the faster it cuts through logs, and the better it handles dense wood species and defects, like knots or areas of tight grain, without bogging down. A more powerful band saw mill also cuts a greater number of board feet per hour, hence is more productive and cost-effective when used regularly
The length of a PBM's bed determines the maximum length of logs that can be cut. Because the cutterhead carriage rides over the log, its track must be long enough for the carriage to clear the log at both the beginning and end of the cut. For example, Wood-Mizer's LT10 mill has a bed that’s 14' 4" long and can cut logs up to 11 feet long.
Fortunately, the majority of band saw mills accept bolt-on bed extensions, allowing them to handle longer logs — up to 25 feet or more. (The rock bottom-priced Lumber Smith PBM requires users to make their own bed and track from construction lumber, which can be built as long as necessary.)/p>
For portability, most smaller PBMs break down into separate components, allowing the mill to be loaded into the back of a pickup truck: The motor/cutterhead carriage detaches from the track and the bed sections unbolt. Alternatively, some models have rigid beds built into wheeled trailers, allowing them to be easily towed.
Manual and Hydraulic
The main distinction between various PBM makes and models is whether they are entirely manually operated or employ hydraulic power. All lower-priced economy models are manual "pushers" (also known as "walkers"). They require the user to either physically push the cutterhead carriage along its track or propel it via a hand cranked cable (some users say they prefer the fingertip feel they get from pushing the carriage, as they're better able to gauge and adjust feed speed when cutting through knots or dense sections of a log).
The setworks on most manual units employs a hand crank mechanism that raises or lowers the motor/cutterhead for setting the depth of cut (gas-filled cylinders found on some models make this operation easier). Log loading, positioning and clamping are also done manually, which requires the help of an assistant for handling all but the smallest logs. A popular option on manual PBMs is a hand-crank-style winch, which mounts to the bed and makes log loading and turning easier.
Larger, more expensive hydraulic PBMs employ a mix of hydraulic and electric power to drive various aspects of the mill's operation. Hydraulically powered cylinders operated by joystick controls are designed to handle a number of different functions, which typically include: lifting and loading the log onto the bed; positioning and clamping the log; turning and repositioning the log between cuts; and more. Electric-motor-powered chains are used on hydraulic PBMs to raise and lower the cutterhead as well as propel the carriage along the track during cutting (carriages on some models have a built-in seat that the operator rides on).
When returning the carriage to its start-of-cut position, some mills have pawls that push the board or slab that’s just been cut, to help offload it. All these electric and hydraulic features are designed not only to make the user's job easier; they increase the productivity of a mill tremendously. Loading, positioning, clamping and turning logs is by far the most time-consuming — and physically exhausting aspect of using a manual PBM. Using hydraulics to accomplish these tasks allows just one or two sawyers to safely cut a significant amount of lumber in a single day.
Controls for all powered functions may be mounted to the mill itself, or located on a remote console, allowing the operator to stand clear of all the noise and sawdust being produced. Computerized consoles on the priciest, most sophisticated PBMs make it very easy to control all the mill's settings and operations.
Cutting with a PBM
Before cutting can begin, any portable band saw mill — manual or hydraulic — must be set up with its bed perfectly straight and flat. Adjustable legs on the bottom of the bed are used to level and stabilize the mill on uneven ground. After the band saw’s blade is tensioned and its guides are set, the log (or a large plank or beam to be resawn) is rolled or lifted onto the bed, using a loader or tractor, the mill's built-in winch or hydraulics, or by hand with a Peavey and a fair bit of muscle. The log is set against two or more vertical side supports, which help orient and stabilize it. If the log is tapered, one end must be elevated, either with shims or the bed’s adjustable toe board, to orient the wood's grain more in line with the bed. One or more clamps are then positioned and engaged to firmly secure the log and keep it from moving during cutting.
With the motor/cutterhead carriage set in its starting position at the far end of the bed, the desired depth of cut is adjusted using the mill's setworks. After the motor or engine is started up, the clutch is engaged to transmit power to the band saw. The carriage is then propelled forward until the blade has cut through the full length of the log. With the clutch disengaged, the slab or board is removed, and the carriage returned to its starting position. If the log is to be cut into slabs, the depth of cut is reset and subsequent cuts are taken. Whether the mill is entirely manual or computerized, the setworks has some kind of indexing device to make it easier to set cutting depth for common board thicknesses (3/4", 1-1/2", etc.) A scale mounted on one of the carriage support posts shows the blade's overall elevation relative to the bed.
If the end goal is to cut the entire log into lumber for construction or furniture, the first cut (or cuts) must remove enough of the log’s bark and sapwood to create a smooth, flat surface. The log is then rotated 90° or 180°, via muscle power or the mill's hydraulic log turner, so that another flat surface may be cut either parallel or adjacent to the first one. Sometimes, this process is repeated until all four sides of the log are flat and square relative to each other, allowing the log to be cut into fully dimensional boards or beams.
After cutting is complete, the freshly cut lumber is offloaded and stacked in the order the boards came from the log. Spacers set under the pile keep the wood off the ground, while stickers placed between the boards allow air to circulate while the wood dries.
Chainsaw Milling Attachments
If you don't have the space or budget for a portable band saw mill, you can still slice up that walnut or oak tree that fell in your backyard by using a chainsaw fitted with a milling attachment. Chainsaw mills such as the Granberg "Alaskan" mill, which sell for between $140 and $250 (not including the price of the chainsaw) provide the most economical way to cut lumber from logs. Their compact size and light weight make them extremely portable, allowing users to cut logs in mountainous or wooded areas that lack any road access. On the downside, a chainsaw mill makes a rougher cut and removes a thicker kerf than that produced by a portable band saw mill.
A chainsaw mill attachment mounts to a regular chainsaw that's been fitted with a longer bar and special rip chain designed to cut efficiently with the wood's grain. A pair of rails on the attachment ride against the log to guide the saw across the log at a consistent depth of cut. A flat board or metal bar temporarily attached to the log guides the initial cut. The rails then ride on the freshly flattened surface of the log for subsequent passes.
The distance between the rails and the chainsaw bar is adjustable and determines the thickness of the planks or boards that are cut. The widest log or plank a chainsaw mill can cut is limited by both the length of the attachment's rails and the chainsaw's bar. Small mills with 18" to 36" rails use a single chainsaw and can be operated by a solo sawyer.
Larger mills with longer rails (up to 56") cut best when powered by two chainsaws, one at each end of a special bar that’s made for the purpose.
Keep the inspiration coming!
Subscribe to our newsletter for more woodworking tips and tricks