Bending Wood Part II - Bent Lamination
We started this wood bending series exploring simple and kerf bending. In this edition, we look at forming wood parts using thin laminates. As we all know, the thinner the part, the easier it will conform to a curve. Lamination is the process of bending many thin parts together and holding them in the desired shape until the glue between them dries. Once dry, the resulting part will pretty much hold its shape forever.
There are two basic ways to clamp the parts while the glue dries; using clamps or a vacuum press, and we will look at both methods.
The obvious first step is to prepare the laminations. For this demo, I used a thin rip jig and zero clearance throat plate to cut a number of thin strips for bending. The thickness of the parts is largely determined by your bend. Shallow curves can be made up of fewer, thicker laminations, while tighter curves need more thin laminations. Once the parts are formed, changing the overall thickness will be very difficult, so take the time to figure out the number and thickness of strips needed to make up your part. If you have a drum sander, getting strips resized is pretty easy, but cutting them to the right dimension on the saw is faster. There are two basic ways to clamp the parts while the glue dries; using physical clamps or a vacuum press, and we will look at both methods.
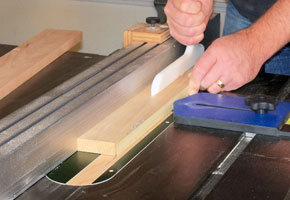
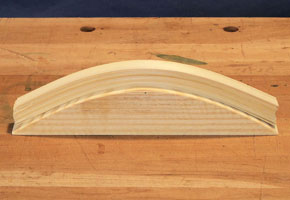
Once you have the stack ready for bending, you need some sort of form to hold them in shape while the glue dries. Whether using clamps or a vacuum press, your form needs to be pretty strong. A lot of force will be exerted to hold the parts and you do not want your form to fail in the middle of the glue up. When possible, I prefer my forms to be solid wood. Being solid pretty much eliminates the chance of having a form fail. When the form needs to be larger, it can be built up.
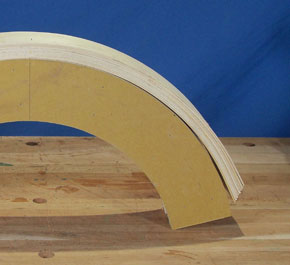
A note on form design here: when you unclamp your dried part, it is going to “spring back” a little bit from the stresses in the bent wood. You may need to over-bend your parts to account for this. There is no formula. A few thick laminations will tend to spring more than many thin pieces. With experience you will get the feel for this, but keep it in mind as you work with your first bent parts. Make the radius of your form just an eighth inch or so smaller than you want to final part to be.
The laminate parts need glue between each layer, and to be clamped to the form before the glue dries. If you are using yellow glue, this does not leave a lot of time. I have found that a mix of 1 part water to 4 parts glue spreads quick, leaves a thinner glue layer which squeezes out less, and gives more open time, all without risking the glue bond.
For this curved apron, I used a form built up from two plywood faces with blocking in between. Clamp the strips to your form in the center and work out to the ends, keeping the work tight to the form. Have lots of clamps on hand, you won’t have a lot of working time after gluing all the pieces. Having the form open in the center allows the clamps to stay perpendicular to the arc. Let the parts set over night.
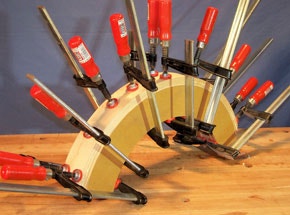
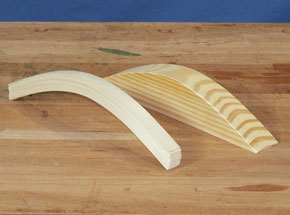
A solid form was used for vacuum clamping this small part. Clamping in a vacuum press applies a surprising amount of pressure evenly across the entire part. When set up right, there will be no gaps in the lamination. With vacuum clamping your form needs to be exceptionally strong or it is likely to crush and ruin your glue up. Vacuum clamping is especially useful for wide parts like curved doors where it is difficult to properly clamp in the center of the part. Many lumber suppliers will sell pretty wide stock already cut into thin pieces that are meant for laminating.
Clamping up simple, fairly shallow curves is a great way to start out and adds a whole new dimension to your woodworking. So far, we have been working with simple forms, but two-part forms can be useful as well.
If you do not have lots of clamps in your shop, a two sided form can effectively clamp up a laminated stack using only a few bar clamps. Two part forms are also essential when your laminated part needs reversing curves.
Keep the inspiration coming!
Subscribe to our newsletter for more woodworking tips and tricks