Green Wood Finishing Products

As environmental sciences get more sophisticated, woodworkers are starting to pay more attention to what finishes they use and what effect they have on the environment.
Green is a popular term these days, used to mean any thing or process that is less damaging to our environment, and ultimately to us. In the finishing world, that entails two very different concepts: green finishes, which are those finishing materials deemed to be either personally or environmentally greener, and green finishing, which deals not with the finishes, but the finishing process.
Since either can give us a healthier environment, I'll talk about both, beginning with green finishes. You should know, though, that the second alternative — green finishing — is a much simpler and cheaper way to go green. It allows us to continue using all the finishes we currently like and still make an impact, and quite possibly the largest impact of all.
Green Finishes
The simple definition of a green finish is one that has a more benign chemical profile than the traditional finish it is designed to replace. What makes them green varies with whoever is labeling them as such. Like beauty, green is often in the eye of the beholder.
For instance, one company I spoke with was dedicated to reducing or eliminating formaldehyde in their formulas. Although the EPA does not restrict formaldehyde as either a VOC or a HAP, it is believed to be a sensitizer that can cause allergic reactions similar to flu symptoms in some people. Others seem unaffected by it. Nevertheless, OSHA, which is concerned not with the environment but with the personal safety of factory workers, has put restrictions on how much formaldehyde they may be exposed to. As a result, the coatings industry has been voluntarily reducing it in their formulas.
Another company formulates their coatings to eliminate anything that might cause any allergic reaction in sensitive people. To that end, they not only reduce VOCs and HAPs, but also other compounds, even inorganic ones, that could cause a reaction. Several companies, in fact, insist they make or sell products that have the least adverse effects on human health and the health of the planet: two concepts that sound good but whose meanings are clearly open to debate. Still others use the term green to mean low VOC coatings, while another group of companies use it to mean coatings made from natural materials, irrelevant of the VOC content.
How Common Wood Finishes Stack Up
Let's look at a few common coatings and see how they stack up. I've listed them more or less from greenest to least green, but be warned: this is not a simple yardstick but rather a complex equation. In many cases, it is a judgment call as to which is really greener, and in some cases we are reduced to splitting hairs. The good news is that no matter what type of coating you like to use, there is probably a greener version of it.
Traditionally Green Finishes
![]() |
![]() |
![]() |
![]() Bulls Eye Shellac |
---|
Some coatings are, and have always been, surprisingly green. Milk paint, for example, contains no VOCs or HAPs and is made of completely natural and sustainable ingredients. Natural oils, such as pure linseed oil and pure tung oil, also fall into this category. Waxes, at least in their solid state, also qualify, since most of the ones we use are either plant waxes, like carnauba and candelilla, or insect waxes, like purified beeswax and shellac wax. However, most paste waxes, the ones that come in tins, contain some VOC solvent to make them softer and easier to apply.
Shellac is another natural, insect-made product that has a very favorable profile. The resin itself is not only renewable, but so harmless as to be edible. The most common solvent for it is ethanol, or grain alcohol, the same alcohol that appears in beer, wine and hard liquor. While ethanol is technically a VOC, it is a slow enough ozone generator that many contend it should be made exempt. In any case, it is relatively safe for the finisher, who at worst runs the risk of becoming inebriated from huffing too many fumes.
Ultra Low and Zero VOC Finishes
Nitrocellulose lacquer, long the darling of furniture manufacturers, contains about 75% solvent, almost all of which is both a VOC and a HAP. Several strategies have emerged to lower that number, sometimes to zero. You can now buy zero VOC lacquer, which oddly enough still contains about 75% solvent. The difference is that it is formulated with exempt VOCs, meaning those that are not ozone generators. Typically, the solvent package is a mixture of parachlorobenzotrifluoride (PCBTF) and acetone, the latter of which appears less harmful to us than some of the solvents it replaces. Thus, zero VOC lacquer may actually be safer to use, not just less ozone generating.
A totally different approach, and one that works particularly well with two-part cross-linking coatings (a specific chemical formulation), is to raise the solids and lower the solvent level. These so-called ultrahigh solids coatings can range from 85% solids to almost 100% solids, the latter containing little or no solvent whatsoever. Typically, these are either chemically cured polyesters or UV cured acrylics and polyesters. Most are designed to be sprayed and are sold only to the industry, not to hobby woodworkers.
Even at that, their safety is a bit of a mixed bag. While they contain almost no VOCs, they carry dangers to the workers indoors. That's because they often emit free monomers that are hazardous. Monomers are resins, not solvents, but the molecule is so small that it can become airborne, and thus can be breathed in. As a result, those who use such coatings generally suit up in hooded coveralls with clean air pumped in to the hood.
Water-based Finishes
Contrary to popular belief, water-based wood stain and finishes are not water-soluble, nor do they contain water-soluble resins. That’s a good thing. If they did, you would be able to remove any evaporative water-based finish with water after it dried. Imagine wiping a counter with a wet sponge and having the finish wipe off. If not water-soluble, then what are they?
Water-based coating are those in which some of the solvents of a traditional coating have been replaced with water. Almost any type of coating can be made water-based; there are water-based lacquers, shellacs, polyurethanes, one and two-part cross-linking coatings, and even water-based UV cured coatings.
Water-based does not mean that the coating contains no solvents. It merely means some of the solvent has been replaced by water. The majority of clear water-based finishes contain glycol ethers, all of which are considered VOCs. While some are quite harmless, others are hazardous to humans, including a very common one, EB (sold under the trade name Butyl Cellosolve), which is believed to be a teratogen (a substance that can cause birth defects). Water-based polyurethanes typically contain nmethyl-2-pyrollidone (NMP) or gamma butyrolactone (BLO) as well as glycol ethers, both of which are also considered VOCs and HAPs.
Still, water-based coatings contain far lower amounts of VOCs than their solvent-based counterparts. For example, a typical nitrocellulose lacquer will contain upwards of 75% solvent, most of which is VOCs, while its water-based counterpart will contain only 10% or less. There are even zero VOC water-based coatings.
Pros and Cons of Water-Based Images
Although water-based coatings are lower in VOCs, clear water-based finishes are also a bit weaker. For instance, water-based polyurethane has about the same abrasion resistance as oil-based, but it has lower solvent, chemical and heat resistance. One could make the argument that if the finish does not hold up as long and you must refinish more often, the extra solvent involved in early refinishing offsets any savings you made initially. Of course, refinishing also means more time and money spent. But there is a way around that. More and more, single-component, self-curing water-based coatings are being offered to kitchen cabinetmakers, and they match oil-based polyurethanes in durability. They've long been offered as floor finishes and are slowly becoming more popular for furniture as well.
While water-based coatings are generally considered greener, there are aspects to them that make them less green, at least in some minds. The resins used in water-based coatings are typically synthesized from petroleum, a nonrenewable resource that has a fairly high carbon footprint, thanks to the energy needed to extract and ship it. By contrast, the resins in oil-based varnish and polyurethane are made from modified linseed, tung or soy oil, all renewable-source plant oils grown right here in the U.S. The tradeoff is natural, renewable, local resins with a higher dose of VOC solvents versus synthetic, foreign imported petroleum-derived resins with a lower dose of VOC solvents. As I said, this is not an easy equation.
Oil-Based Finishes
Danish oil, teak oil, spar varnish and the whole field of oil-based varnishes and polyurethanes, both liquid and gel, make up the next category. In general, these wood finishes are relatively safer for us than for the environment. They contain ozone-generating VOC solvents, and thus are not good for the environment. However, the ones they contain, such as mineral spirits, are fairly safe for us, at least in the limited amounts to which we are exposed. Their high solids content, often 45% or so, means what solvents they do contain are in more limited amounts than what you would find in lacquer, for example.
Although the solvents are petroleum-based, the resin portion is made from natural seed oils, usually linseed, soya or tung. Such oils are renewable crops grown here in the U.S., and they require little processing to go from raw oil to resin. What's better is that these coatings are almost never sprayed, but rather are applied either by brush, or by wiping on and off, as in the case of Danish oils and gel polyurethanes. Those application methods have a very high transfer efficiency, which means very little is wasted and only a minimum of solvent is used.
Traditional Lacquer, Etc.
Traditional lacquer contains lots of VOCs and HAPs, some of which are not only strong ozone generators but are harmful to humans as well. These solvents are also usually quite flammable, providing yet another safety issue. What is worse is that they are typically formulated for spraying, a very wasteful application process that not only wastes coating, but also uses up a lot more solvent in both thinning and cleanup. Catalyzed lacquer, conversion varnish and precat lacquer have all of the above disadvantages and may contain formaldehyde and hazardous acids as well. For that reason, these coatings are considered the least green option.
Steps Toward Green Finishing
I promised you that there is an easier, cheaper alternative that lets you use nearly any finish and still come out greener. It's called green finishing. The good news is that by slightly changing the way you use finishes, you can be greener and save money to boot. Green finishing employs two means to lower VOCs: reducing waste, often through low-tech application, and recycling solvents.
The Application Method You Choose Can Reduce Waste
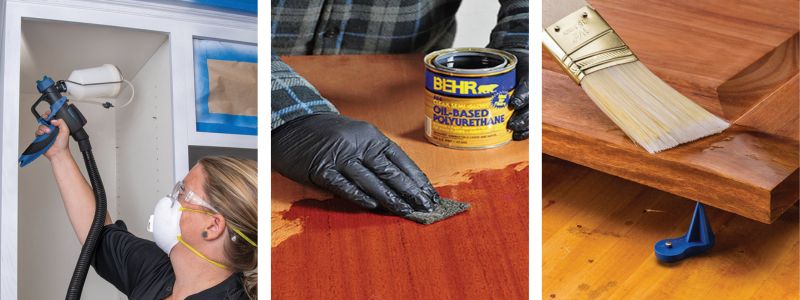
The first step in reducing waste is to buy wisely. In other words, try to buy only the amount of finish you need for the job. Too often, leftover finish ends up crusting over or otherwise going bad and gets thrown away. That does neither the environment nor your pocketbook any favors. A less obvious way to reduce waste is to choose an application method with a high transfer efficiency. Transfer efficiency is the percentage of the finish you buy that actually ends up on the wood.
Finishing Sprayers - Most standard spray guns have about a 25% transfer efficiency, meaning about 75% of the finish gets wasted, mostly blown out through the spray booth fan or trapped on the filters. Even those systems that boast higher transfer efficiency, such as HVLP turbine rigs, only reach about 65% transfer efficiency. That's still a lot of waste.
Wipe-On Application - Compare that with a wipe-on gel polyurethane. If you're like me, you apply it with a piece of nylon abrasive pad. One pad will do an entire roomful of furniture without wearing out, and when you are all done, very little remains on the pad to be dried out and thrown away. The waste comes only in how much you wipe off, and with attention, you can keep that to a minimum as well. Since applicators and wiping rags are allowed to dry out, then get thrown away, there is no solvent used for cleanup.
Brush-On Application - Using a brush to apply finish approaches near 100% transfer efficiency. The only amount of finish that does not make it onto the wood is the tiny bit you must clean out of the brush bristles when you are all done. As for the cleaning solvent, that can be kept to a minimum through recycling.
Recycling Solvents
That brings us to the other way we can be greener no matter what finish and solvent we use. Solvents may not be forever, like diamonds, but they are reusable again and again. The mineral spirits you use to clean your brush or the lacquer thinner you use to clean spray guns can be poured into a lidded container and shelved. Over time, the heavier foreign matter will settle to the bottom. When that happens, decant the clearfix liquid atop and reuse it for cleaning the next brush or gun. You will lose some each time to evaporation, but you will be surprised at how much you can reduce your VOC consumption by recycling your cleaning solvents.
By now it should be obvious that by avoiding waste and recycling solvents, you not only reduce your carbon footprint on the earth, but also save money in your wallet. After all, if you are buying fewer cans of finish and solvent, you are coming out ahead in every way.
Keep the inspiration coming!
Subscribe to our newsletter for more woodworking tips and tricks